
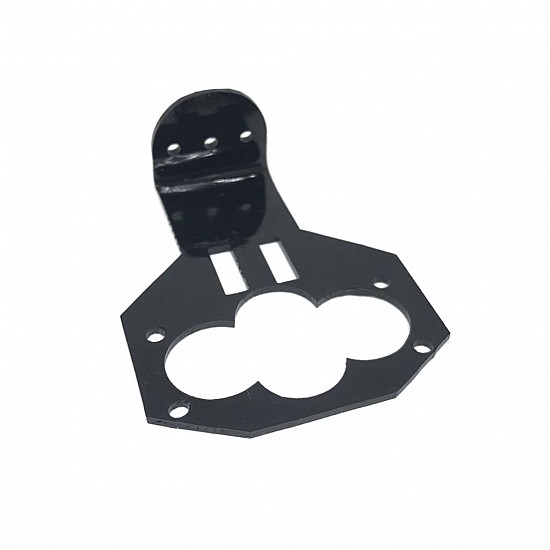
- Mount frc ultrasonic sensor pro#
- Mount frc ultrasonic sensor code#
- Mount frc ultrasonic sensor series#
You might consider performing this process before using your robot the first time it is used within a new environment (e.g., when you arrive at a FTC competition event). NOTE: It is very important to hold VMX still, and parallel to the earth’s surface, during this Initial Gyro Calibration period. When VMX is re-started, it will perform the Initial Gyro Calibration – the same process that occurs at our factory. When you release the “CAL” button, ensure that the “CAL” Led flashes briefly, and then press the “RESET” button to restart navX-Micro. Therefore, since the average ambient temperature at the factory (on the island of Kauai in Hawaii) may be different than in your environment, you can optionally choose to re-calibrate the gyroscope by pressing and holding the “CAL” button for at least 10 seconds. Note that the onboard gyroscopes are sensitive to temperature changes. Calibrating and Using the navX-sensor IMUīefore VMX units are shipped, the accelerometers and gyroscopes are initially calibrated at the factory this calibration data is stored in flash memory and applied automatically to the accelerometer and gyroscope data each time the navX-Micro circuit board is powered on.
Mount frc ultrasonic sensor pro#
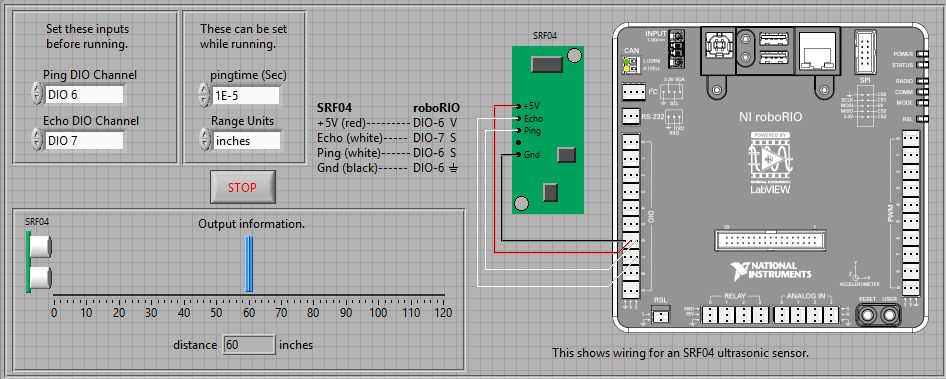
Connect the ground wire to the other side of the potentiometer and to the V- pin on the IC. Connect the 5V supply to one side of the potentiometer and to V+ pin on the IC. All you need is a 741 op-amp IC and a potentiometer (variable resistor). If you don't have an Arduino, you can use an op-amp (operational amplifier) to monitor the signal from the proximity sensor.
Mount frc ultrasonic sensor code#
Example Code int InputPin = 0 // analog pin 0 is the input pin int OutputPin = 1 // digital pin 1 is the output pin int val = 0 // variable to store the value read void setup() Here is an quick example of the code that you could use. When the voltage drops below a set threshold, the Arduino activates the your special effects. The AnalogRead function measures the voltage of the signal coming from the sensor. Then connect the signal wire from the sensor to an analog input pin on the Arduino. Connect the 5V wire from the sensor to either the 5V pin or a digital output pin set to HIGH. To do this, connect the ground terminal from the sensor to the GND pin on the Arduino. In most cases you will use a microcontroller such as an Arduino to monitor the signal from the sensor. This also helps to make the sensor more directional. The most effective way to do this is to put a black piece of heat shrink tubing around the phototransistor. To ensure that only reflected light is detected by the phototransistor, it is important to add a light barrier between the LED and the phototransistor. I added three pins to connect the sensor to the signal processor. I soldered the sensor components together on a small piece of perf board. An additional wire is connected to the collector to act as an output pin for the sensor. The collector is wired to a 10 kohm resistor that is connected to 5V. The emitter of the phototransistor is connected to ground.
Mount frc ultrasonic sensor series#
Or you can use multiple LEDs in series to bring down the voltage across the resistor. You can use two 68 ohm resistors in parallel. If you don't have a resistor rated for that much. A 33 ohm resistor will experience about 1/2 watt if power. The closest resistor that I had above this value was a 33 ohm resistor. To find the appropriate resistor value for the LED use this formula: Resistor Value = (Supply Voltage - LED Voltage) / LED Current. The IR LED is connected to the 5V supply with a 33 ohm series resistor.
